Swagging, also known as end pressing, is a specialised metal forming process used to alter the shape or cross section of the ends of metal profiles. in some cases, it can be used to change the cross section in the middle of a metal profile.
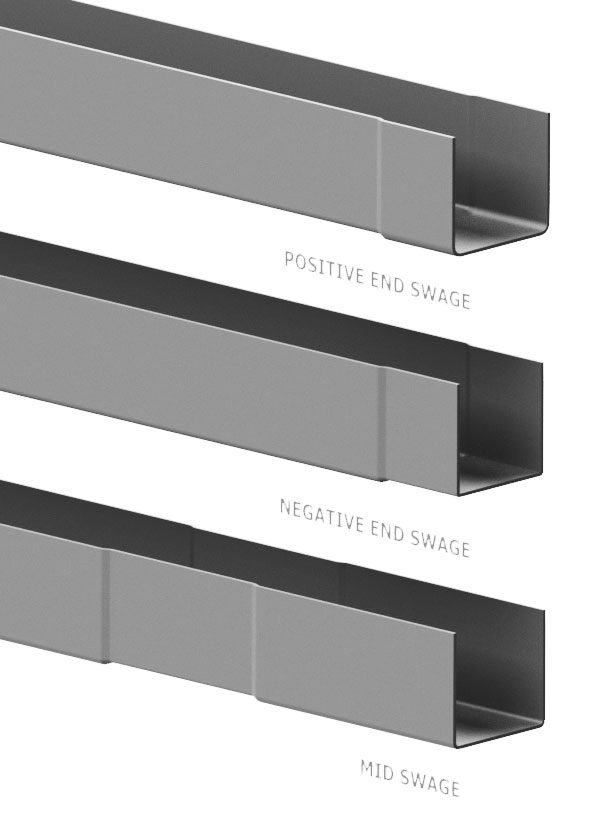
This process is commonly employed to create tapered or expanded ends, adjust diameters, or form specific shapes that meet precise engineering requirements. Swagging can be integrated into the cold roll forming process or executed as a subsequent operation.
Applications of Swagging in metal profile manufacturing
- Solar Industry: Roof and ground mounted solar framing systems comprise a large number of connections. Swaging the metal profiles which make up these structures can significantly reduce the number of fasteners and fixtures needed to install these; speeding up installation time and reducing cost and the need for tooling on site.
- Automotive Industry: Swagging is used to create joints, connectors, and fittings for exhaust systems, drive shafts, and other components.
- Aerospace: In aerospace applications, swagging is utilized for producing precise and strong connections in airframes, hydraulic lines, and structural components.
- Construction: Swagged metal profiles are used in construction for frameworks, scaffolding, and other structural elements that require strong and secure connections.
- Manufacturing: It is employed in the manufacturing of furniture, lighting fixtures, and various equipment requiring custom-shaped metal parts.
- HVAC Systems: Swagging is used to form connections and transitions in ductwork and piping systems for heating, ventilation, and air conditioning.
Key Considerations
Tooling Design: Custom tooling is crucial for achieving the desired end profile. We design and manufacture tooling to match your exact specifications, ensuring uniform and accurate deformation.
Quality Assurance: Post-swagging, each profile undergoes thorough inspection to verify dimensional accuracy and surface quality. We employ rigorous quality control measures to ensure that all profiles meet your stringent standards.
Process Control: Both inline swagging and offline operations are monitored using advanced control systems to maintain consistent pressure, speed, and alignment. This ensures high-quality results.
The Swagging Process
Initial Profiling: Flat metal strips are fed from a coil into our advanced cold roll forming lines, where they are progressively shaped into the desired profiles with high precision and consistency.
Inline Swagging | Swagging Offline |
---|---|
Integrated Deformation As part of the continuous roll forming process, the metal profiles pass through specialized stations where swagging occurs. During this inline step, precise radial deformation is applied to achieve the required end shape or cross section change. The integration of swagging into the roll forming line ensures seamless processing and maintains high throughput. | Setup and Positioning Once the profiles are formed, they are positioned in an offline press cell. Accurate clamping and alignment ensure that the profiles remain stable during the swagging process. Offline Swagging The press applies controlled pressure to the ends of the profiles, deforming them to the specified shape or cross section. This method allows for precise adjustments and is ideal for profiles that require specific end treatments post-roll forming. |
By integrating swagging either inline within the roll forming process or as a subsequent step, we offer flexible and precise solutions to meet your specific engineering requirements. This approach ensures efficient production while maintaining the highest quality standards.
Get in touch
Your project aims are at the heart of our approach. Our engineers are on hand to work with you to meet your clients needs and achieve the optimum balance of cost and performance.