PROS & CONS OF COLD ROLL FORMING
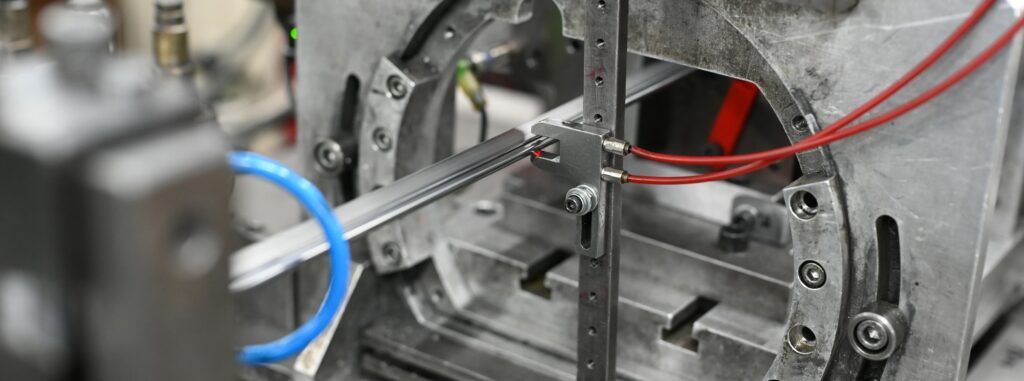
Cold roll forming is a manufacturing process used to shape metal materials into complex profiles with consistent cross-sections. Like any production method, cold roll forming has its own set of advantages and disadvantages.
Pros of Cold Roll Forming:
- Cost-Efficient: Cold roll forming can be more cost-effective than other metal forming methods, such as hot rolling or extrusion, due to its lower energy consumption and reduced material waste.
- High Production Rates: The continuous nature of cold roll forming allows for high production rates, making it suitable for large-scale manufacturing.
- In-Line Processes: With cold roll forming it is possible to integrate processes in-line. A few examples are: in-line hole punching, bending, laser welding, swaging, foiling and customer specific assembly’s.
- Long Part Lengths: Cold roll forming can be used to produce parts as long at 16m in length.
- Consistent Dimensions: Cold roll forming produces profiles with precise and consistent dimensions, ensuring high levels of uniformity across the entire production batch.
- Design Flexibility: It enables the creation of complex cross-sectional shapes and custom profiles to meet specific design requirements, in a wide variety of formable metals
- Material Savings: Cold roll forming often requires thinner materials compared to other forming methods, leading to material savings and reduced overall weight of the final product.
- Improved Material Properties: The cold forming process can enhance the mechanical properties of the metal, making it stronger and more durable.
- Reduced Residual Stress: Cold roll forming generates less residual stress in the metal compared to hot rolling, which can be beneficial for certain applications.
- Minimal Surface Imperfections: The controlled forming process reduces surface imperfections and defects, resulting in a smooth finish.
Cons of Cold Roll Forming:
- Initial Tooling Costs: The setup costs for creating custom roll forming tooling can be relatively high, making it less economical for small production runs.
- Lead Times: custom profiles may require dedicated tooling to be designed and manufactured, which can add to the lead time of new product introduction.
In summary, cold roll forming offers numerous benefits, including cost-efficiency, high production rates, and consistent dimensions. However, it may have some limitations related to tooling costs, and profile complexity. The decision to use cold roll forming should consider the specific requirements of the project and the material properties needed for the final product.
At Hadley, we have a team of over 50 in-house engineers to work with you on your profile and tooling needs. Having this function internally helps us reduce lead times, as we design, make and test the tooling in our own dedicated bay. Find out more with this short video on our capabilities.
If you would like to discuss your project or have a tour of our engineering and testing facility, please drop us an email and we can find out if cold roll forming suits your project.
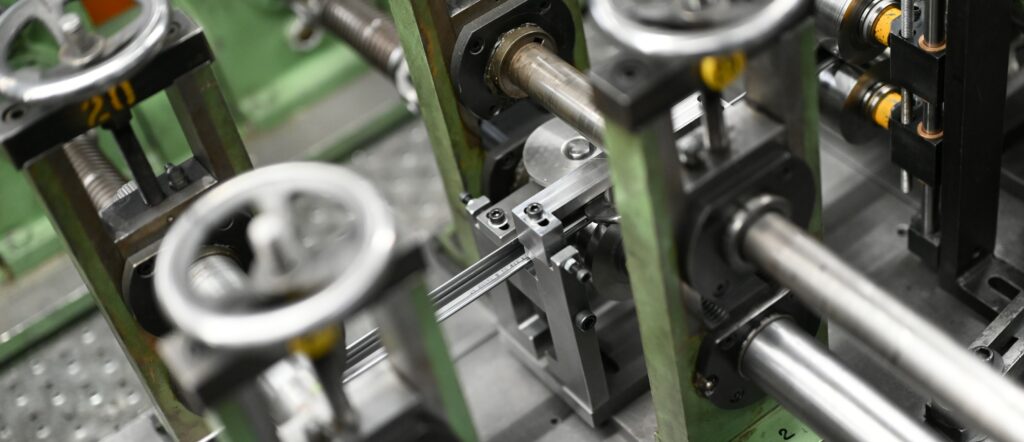